Purified Water Needs the Right Tools Now
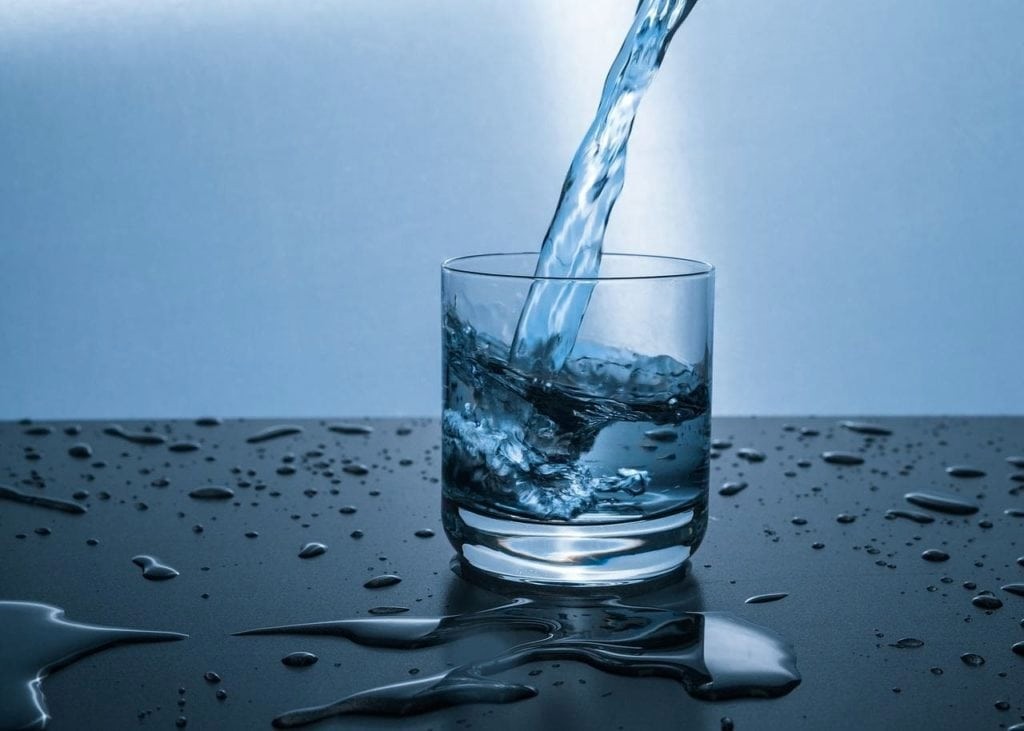
Sintered metal media are used in numerous industrial liquid and gas filtering applications to separate particle materials (liquid or solids and gas or solid separation). Chemical filtration uses sintered metal filters manufactured from fibers or powdered metals formed into filtering components. Environmental guidelines require the removal of particulates to protect downstream equipment.
Look For Your Best Deals
Sintered metal blocks downstream processes. Sintered metal media have been found to efficiently remove particles, filter reliably, and last a long time. These filters can capture 99.9{d2862e6e2d69dd67fc7e121421cd8c1e934bb4a7696309954b9c432b55e5f955} of particles using surface or depth media. Depending on the alloy, operating temperatures may approach 1000°C. Beyond filtering efficiency, corrosion resistance, mechanical strength at service temperature, cake release (blowback clean ability), and long-term service life are important properties. Addressing these issues is critical to efficient operations. The water filters are most important parts of these purifications and the sintered filter cartridge is the best deal here.
The filter medium’s particle holding capacity and pressure drop dictate the filter’s operating life. This cake may be removed using a blowback cycle. The effectiveness of the cake and filter media in the blowback cycle and recovery of the filter pressure reduction.
Polishing Filter with Depth Filtering Medium
Back-washable media reduces operator exposure to process materials and contaminants while improving filtering efficiency. Regardless of temperature or corrosiveness, sintered metal filtration may benefit any pressure-driven filtering operation with high operating expenses. This study will examine sintered porous metal media and filtering system design requirements to increase chemical process stream performance.
Entering a New Millennium with Many Economic and Environmental Challenges
As a result of changing worker requirements and the globalization of the market, change is inevitable. The chemical processing industry’s future competitive advantage will be patented technologies. New processes will be developed that are low-cost, high-yield, and high-quality, while also being low-impact and energy-efficient.
Solids (particulate) handling is important in the chemical industry. Filtration employs a distinctive filter design and a unique system operating approach to decrease solids. Filtration can improve product purity, increase throughput, and reduce or eliminate polluted effluent. Continuous filtration technologies have replaced batch filtration processes. The innovative method also saves labor expenses by reducing hazardous waste. Fully automated filter systems can be integrated with plant process controls.
Solids reduction includes cleaning solvents and process effluent waste streams, as well as solids removal. The recovered liquid product may be utilised as a chemical feedstock. Hazardous solids may be recovered or recycled whereas non-hazardous solids can be reduced to landfill. Filtration can reduce BOD, COD, TSS, and TOC (Total Organic Carbon) (Total Organic Carbon). These are the most significant factors to examine when analyzing the current condition of air pollution emissions.
Filtration Basics
Understanding filtration principles is crucial to selecting the right media and filter design for each filtering application. Deep and surface filtering are two popular methods. Surface filtering, as opposed to depth filtration, produces a particle cake when particles are retained at the media’s surface for subsequent collection.
Surface filtration occurs when particles larger than the filter media’s pore size are sieved at the filter’s upstream surface. Because of their size, particles cannot enter or exit pore holes. As additional particle-laden fluid is injected into the filter medium, the particle cake thickens. If the cake’s pores are smaller than the filter medium’s, it may assist separate finer particles. The cake’s porosity must be sufficient to continue filtering. Processes may be conducted with constant pressure or decreasing flow. Because most surface filters are not perfectly smooth or have uniform pore structure, depth filtering may occur, reducing filter life.